:::
科技新知
電動車帶領PCB技術再進化
發表日期:2022-12-21
作者:張淵菘(工研院)
摘要:
近年淨零碳排已是國際共識,全球主要經濟體皆已宣示其執行決心,如美國、歐盟及日本訂定2050年達全面碳中和,中國大陸則訂定2060年達碳中和。
全文:
一、全球電動車市場發展概況
近年淨零碳排已是國際共識,全球主要經濟體皆已宣示其執行決心,如美國、歐盟及日本訂定2050年達全面碳中和,中國大陸則訂定2060年達碳中和。由於交通運輸工具的碳排量僅次於工業,因此發展電動車已成為各國淨零碳排的重點策略。在環保意識與政府政策的推動下,全球電動車的銷售量正快速攀升,2021年是全球電動車(包括純電動式、油電混合式、燃料電池式等)銷售量與成長率最高的一年,共約為660萬台,年成長113%,占當年度整體汽車銷量8.6%,而這個比例在2017年僅為1.4%,可見其發展趨勢強勁。以國家區分,前三大銷售市場為中國大陸、歐盟、美國,其中中國大陸約占50%市佔率,並為全球電動車最大的生產與銷售國。
今年由於受到俄烏戰爭與中國封控影響,通膨高漲與供應鏈斷鏈危機讓全球電動車成長趨緩,但不像消費性電子市場衰退,今年應能維持正成長,預估2022年全球電動車銷售量可達810萬台,年成長22.7%,占整體汽車銷量為10.8%。
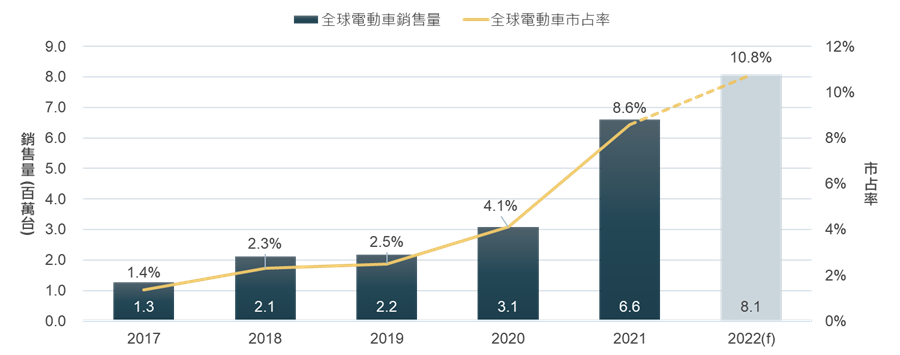
資料來源:工研院產科國際所ITIS研究團隊(2022/12)
圖一、全球電動車銷售趨勢
二、電動車帶動車用PCB用量增長
EEA(Electrical/Electronic Architecture),又稱電子電氣架構,可以理解成汽車所有使用到的電子與電氣零件,以及各零件之間的結構布局與系統設計。過往車輛EEA為「分散式」架構(Distributed),每一項車輛的功能都由獨立的ECU所控制,ECU(Electronic Control Unit)是電子控制單元,其組成零件有MCU(微控制器)、PCB等。隨著自駕與智慧座艙的技術不斷升級,以及對5G的高速傳輸需求,車輛的功能設計越來越豐富,ECU數量也越來越多,這使分散式EEA已無法滿足日趨複雜的系統設計,同時也存在成本過高與資安風險等問題。
所以各大車廠逐漸往「域集中式」(Domain Centralized)EEA發展,除具備結構簡化、高拓展性、算力集中等優點,還可執行OTA(空中下載技術)升級,賦予汽車「時用時新」的駕駛體驗,是傳統功能車轉型電動車的關鍵發展。域集中式EEA是根據汽車功能劃分若干領域,如車身控制域、自動駕駛域、智慧座艙域等,功能相似的ECU將整合成性能更強大的單一ECU,並透過域中心控制器協調整合,以實現更複雜的功能。而這類具有整合性、多功能、高效能等特性的ECU,對其相關PCB的使用量與技術需求也有所提升。
不過由於目前電動車的滲透率還不高,所以車用PCB的使用量還是以燃油車為主,約佔八成的比重,但以單輛車來比較,電動車的PCB使用量會比燃油車還來得多。大致上,燃油車每輛車的PCB平均用量約為0.5m2,HV(油電混合車)的PCB使用量介於0.5~1m2,而PHV(插電式油電混合車)/EV(純電動車)/FCV(燃料電池車)等的PCB使用量則在1m2以上。隨著電動車持續普及,帶動其PCB使用量增加,預估到2030年,電動車將成為車用PCB的主要應用,比重達63%,而整體車用PCB的使用量也將從2019年的4,720萬m2成長到2030年的8,289萬m2,期間平均年複合成長率為5.2%。
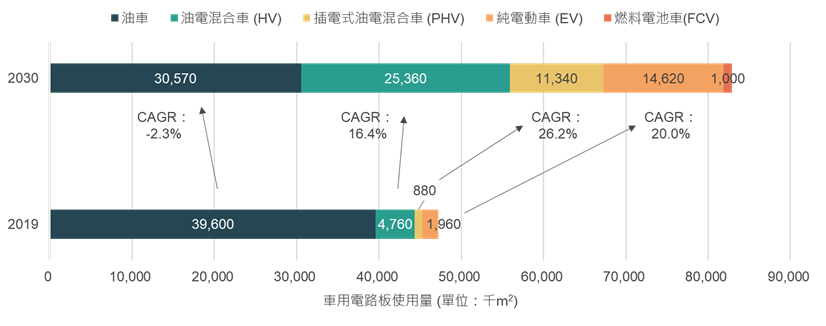
資料來源:富士キメラ総研 & CMK
圖二、車用PCB需求量成長預估
三、臺灣車用PCB發展概況
2022年上半年臺灣PCB製造產值統計約為4,197億新臺幣,若再依應用市場區別,應用於車用PCB產值約為473億新臺幣,占整體產值為11.3%。由於車用晶片的短缺尚未趨緩,整車產能依然受到限制,以及市場前景不樂觀,使得今年全球汽車市場銷售量持續衰退。但由於汽車持續朝電子化趨勢發展,使車用電子產品增加,連帶提升車用PCB數量。因此儘管市場銷量不振,但臺灣在車用PCB還能維持成長,統計今年上半年產值較去年同期成長8.2%。
臺灣車用PCB目前以多層板為主,約占63.5%比重,主要廠商包括敬鵬、健鼎、精成科等,其中敬鵬為全球第四大車用PCB廠商;臺灣第二大車用PCB為HDI,約占15.8%比重,主要廠商包括健鼎、燿華等;另外還有軟板與載板等產品在車用PCB市場占有一席之地。
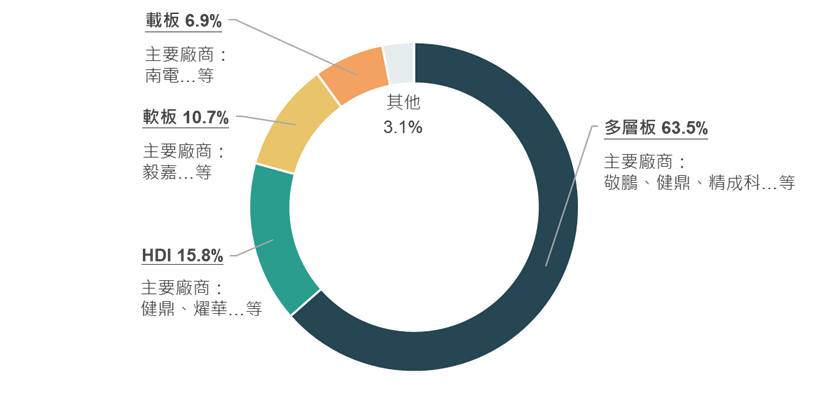
資料來源:TPCA & 工研院產科國際所ITIS研究團隊(2022/12)
圖三、臺灣車用PCB產品結構分布 (2022H1)
四、車用PCB技術發展趨勢
未來車用PCB發展將主要往小型化、高頻、高密度、高功率等趨勢發展,包括載板、HDI與軟板都是廠商積極切入的開發重點。以下將概述此三項車用PCB的技術發展趨勢。
(一)車用載板
目前車用載板大多應用在ECU、影音娛樂及通訊等晶片封裝上,產品以BT載板為主。因應車聯網、5G/B5G通訊技術,及產品模組化發展趨勢,未來車用BT載板將會往小尺寸、多層數、高佈線密度等方向設計。
此外,隨著自駕車技術不斷進步,自駕等級從2020年Lv3 (有條件自動化),預計在2025年提升至Lv4 (高度自動化),到2030年將有望達到Lv5 (完全自動化)。為滿足自駕需求,車身設計將會安裝大量的攝影機與光學雷達等感測器來偵測周遭環境與車輛位置,同時也會需要HPC(高效運算)平台做為車輛的CPU使用,高效即時地處理所收集的數據,並規劃與執行可安全行駛的道路。
這些CPU、GPU等高效運算IC會使用ABF載板做為晶片封裝基板。ABF是由日商味之素(Ajinomoto)所開發的高階載板增層材料(Ajinomoto Build Film),具有高耐用性、低熱膨脹性與易加工等特性,並且能夠用SAP(全加成法)的PCB線路製程製作極細的線路等級(線寬約8~15um),因此適合高腳數高傳輸的IC封裝,目前ABF載板已成為FC-BGA封裝標配。
為滿足高階算力升級與需求增加,小晶片(Chiplet)異質整合封裝技術是未來的發展趨勢,可以把來自不同FAB、不同製程節點與不同屬性的晶片整合成單一顆晶片,能提供IC設計業者更高的設計彈性。這除了會擴大ABF載板的面積外,封裝元件與I/O數增多也會讓ABF載板的線路設計更細更密集、層數也同步增加,整體製作難度將大大提高。
臺灣在ABF載板的技術發展趨勢大致朝層數提升,由18層增加至24層,板厚也隨之增厚;而為了讓線路設計更密集,線寬與雷射盲孔將持續縮小,線寬朝8/8um開發,雷射孔徑則以35um為目標,這2項是現階段PCB產品以量產為前提下最高階的技術要求。
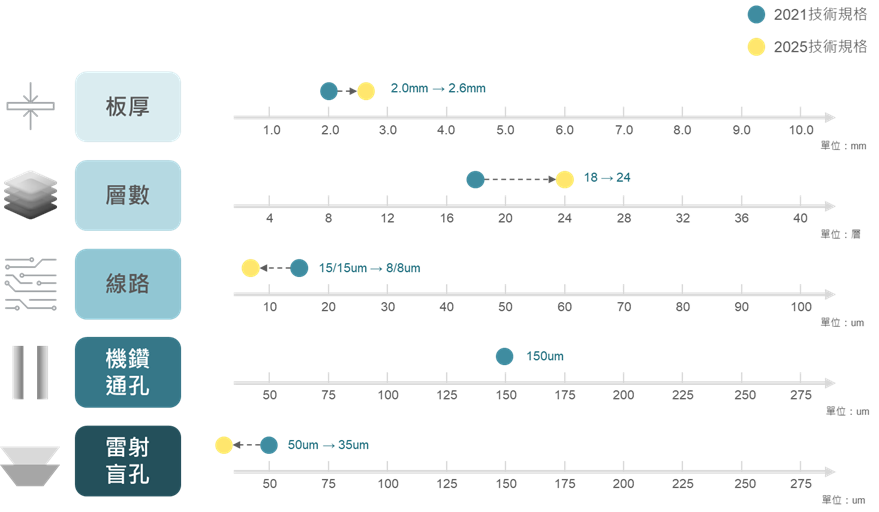
資料來源:TPCA & 工研院產科國際所ITIS研究團隊(2022/12)
圖四、臺灣ABF載板技術發展趨勢
(二)車用HDI
目前車用PCB雖以大尺寸多層板為主,但隨著車輛電動化、自動化,以及對5G車聯網的需求,使車用PCB逐漸朝向小型化、高密度、高頻及高功率等趨勢發展。
在自動化相關的車用產品,如毫米波雷達、車用感測器、通訊模組等,產品會往小型化、高效能發展,因此對PCB的設計會以HDI為主,並著重在線路密度與精度提升,除使用高階數或Anylayer(盲孔連接任意層)結構,同時也會採用mSAP(半加成法)細線路製程與小孔徑雷射加工製程。而因應雷達與通訊產品的高速傳輸需求,高頻PCB材料或hybrid結構等是未來設計趨勢。其中hybrid結構是指將一般基板材料與高頻基板材料混合使用,只在訊號層使用高頻材料,其他層別則使用一般材料,可降低材料使用成本並兼顧訊號傳輸品質,但反之則須克服異質材料同時加工的問題。
而在PCU(功率控制單元)、IPM(智慧功率模組)、BMS(電池管理系統)等高功率相關的車用產品,由於常處於大電流、高電壓與高放熱的工作環境,因此相關PCB會朝厚銅、內埋式銅塊或放熱元件、以及金屬基板等可強化散熱效率的設計開發。

資料來源:定穎、ISU Petasys、Meiko
圖五、車用PCB技術應用
(三)車用軟板
車用軟板目前可應用在傳動系統、照明系統、感測器、零件切換開關、車載資訊娛樂系統、以及BMS(電池管理系統)等,由於對自駕功能與智慧座艙的需求增加,車用軟板將著重在高頻化與高密度化的趨勢發展。因應高頻化,在4G時代常用的軟板材料PI(聚醯亞胺),其Df值(介電損失)已無法滿足5G訊號傳輸的需求,正逐漸被MPI(改質聚醯亞胺)、LCP(液晶高分子)、氟素材料等新型高頻軟板材料取代,其中LCP兼具材料成本與特性表現的優點,是目前在5G毫米波頻段中被主流使用的高頻軟板材料。隨著續往6G或衛星通訊發展,擁有極低的Dk(介電常數)、Df特性的氟素材料是未來研發的重點,包括了PTFE(聚四氟乙烯)、PFA(可溶性聚四氟乙烯)、AFMPI(高性能聚醯亞胺)等材料,除更佳的高頻特性外,亦可直接在傳統軟板製程使用,無須開發新製程,但因材料內含有氟素,會影響材料表面的黏著強度,是未來導入量產的一大挑戰。
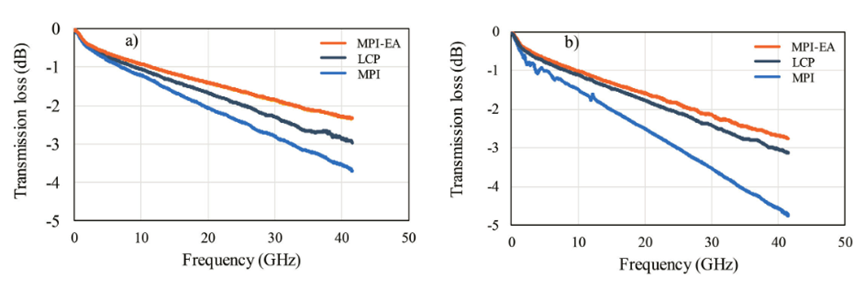
資料來源:AGC
圖六、分別在標準條件(圖a)與高溫高濕條件(圖b)測試下,氟系材料AFMPI(MPI-EA)的介電損失表現較LCP與MPI好
應用在BMS的車用軟板是另一個發展重點。為了精準量測電池電壓,避免電池過放電、過充電及過高溫,電動車的電池模組設計將更為龐大且精密,也讓車用軟板的長度越做越長,雖然製作難度提高,但也進一步增加車用軟板的使用量。
五、結論
隨著汽車電子電氣架構升級、自駕技術與智慧座艙功能不斷演進,以及在5G通訊助力下,汽車已從傳統運輸工具進化成大型終端設備,就像電腦與手機一樣,未來將成為我們日常生活與工作生產的一部分。同時在環保浪潮推動與國際政策獎勵下,電動車的銷售正快速成長中,加上功能日趨豐富複雜,所使用的電子元件越來越多,都進一步推升車用PCB的使用量增加與技術升級。
未來車用PCB發展將主要往於小型化、高頻、高密度、高功率等趨勢發展,包括載板、HDI與軟板都是廠商積極切入的開發重點。而為因應產品趨勢,在車用PCB技術研發上會擺脫傳統厚大板的設計,逐漸往手機產品看齊,包括開始使用細線路製程mSAP或SAP,雷射盲孔尺寸也會逐漸縮小,高頻材料的車載應用越來越頻,而高功率的工作環境,也讓車用PCB有加強散熱效率的設計需求。
(本文作者為工研院產科國際所執行產業技術基磐研究與知識服務計畫產業分析師)
點閱數:
4506