:::
科技新知
全球鋼鐵業碳排現況與低碳化發展動向
發表日期:2023-10-04
作者:陳建任(金屬中心)
摘要:
鋼鐵業是能源密集型產業,也是CO2的排放大戶。根據世界能源總署的統計,2020年全球鋼鐵業的直接碳排放總量約為26億噸,占全人類活動碳排放總量的7~9%,是主要碳排放源之一。
全文:
一、全球鋼鐵業碳排現況與特徵
鋼鐵業是能源密集型產業,也是CO2的排放大戶。根據世界能源總署的統計,2020年全球鋼鐵業的直接碳排放總量約為26億噸,占全人類活動碳排放總量的7~9%,是主要碳排放源之一。因此,在推進全球碳中和的進程中,鋼鐵業是重要關鍵產業之一,負有重大減排責任。
2022年12月世界鋼協發佈了「2022年永續發展指標報告」,該報告對83家鋼廠與協會的資料進行統計,結果顯示2007~2021年間,世界鋼協會員廠的平均每生產一噸粗鋼大約排放1.75~1.91公噸的CO2。噸鋼能耗多維持在19.51GJ~21.31GJ之間,詳細數據如【圖1】所示。上述指標反映了世界鋼協會員廠的碳排放平均水準,惟各家鋼廠的生產技術、生產規模、投入原料、電力碳排係數等條件並不相同,各家鋼廠的碳排放密集度及能源強度會有明顯差異。【圖1】為2007~2021年全球鋼鐵業粗鋼產量、CO2排放強度、能源強度趨勢。
目前國際鋼鐵業碳排放主要存在以下特徵:
(一)同一鋼鐵企業噸鋼CO2排放量不一定是逐年降低的,雖然各類節能降碳技術不斷普及應用,惟噸鋼CO2排放量還與當年企業的產品結構、使用能源結構、原料/燃料品質以及管理水準等密切相關。
(二)不同鋼鐵企業的噸鋼CO2排放資料不能簡單地進行直接比較,因為各國家地區原料條件(廢鋼、鐵礦、煤礦、直接還原鐵等)不同,各鋼鐵企業生產流程 (高爐/轉爐、電爐、天然氣直接還原煉鐵等)結構不同、能源結構(煤炭、天然氣、電力)不同,甚至其CO2排放的計算方法、統計和範圍都存在差異,因此僅比較CO2排放指標來評價孰優孰劣,是不科學的。目前全球主要國家正針對CO2的排放計算方法、標準化等相關工作,進行探討與研究。
(三)相較於高爐-轉爐流程而言,電爐煉鋼流程的噸鋼CO2排放要小得多,但其生產產品卻有限制。調整生產流程結構、發展全廢鋼電爐流程是鋼鐵行業減排的有力措施,但須考量電爐所生產出來的產品是否符合後續的加工需求。
(四)整體而言,各鋼鐵企業CO2排放總量降幅較小,部分企業甚至有上升趨勢。因此,鋼鐵行業依舊面臨著嚴峻的減碳壓力。
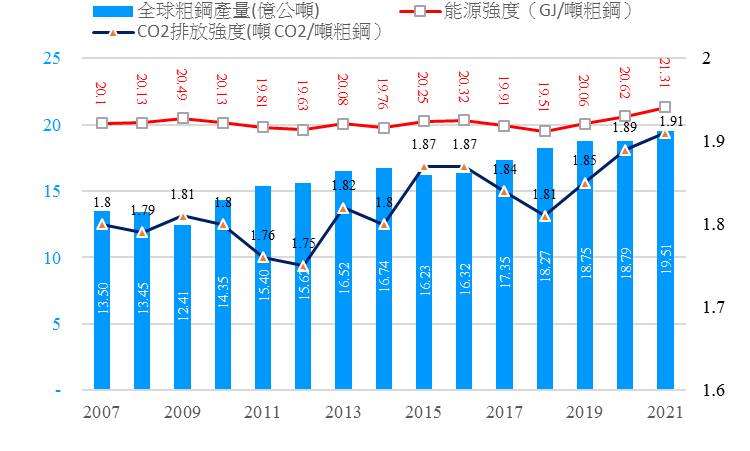
資料來源:worldsteel/金屬中心MII-ITIS研究團隊整理
圖1、全球鋼鐵業粗鋼產量、CO2排放強度、能源強度趨勢
二、鋼鐵業低碳化主要方向與策略
為因應嚴峻的減碳壓力,未來鋼鐵業低碳發展的主要方向及策略有以下幾點:
(一)提高電爐煉鋼比重
相較於高爐/轉爐流程,電爐煉鋼無論是在能耗水準,還是在減少CO2排方面均具有一定的優勢。高爐/轉爐流程生產1公噸粗鋼,約產出2.2公噸二氧化碳,電爐煉鋼1公噸CO2排放只有0.4~0.6公噸,亦即高爐/轉爐流程的排碳量約為電爐流程的五倍,相同的鋼材從高爐改採電爐生產,減排幅度高達8成。若能使用綠電供給電爐設備進行冶煉,其減碳幅度更為可觀。惟電爐製程較不適合生產薄板類等鋼材,除非掌握高級廢鋼或低碳直接還原鐵之冷鐵源。現階段由於低雜質冷鐵源不足,大量將高爐/轉爐製程設備轉換為電爐流程,可能造成全球薄板類等高級鋼材供應不足。
(二)氫冶煉技術與設備之研發與建置
歐盟超低二氧化碳排放煉鋼工藝研究專案(Ultra-low CO2 steelmaking,ULCOS)是已知的氫基煉鋼最早的綜合研究專案。此外,日本COURESE50項目、瑞典HYBRIT項目、奧地利Voestalpine鋼廠的H2FUTURE項目,SSAB、LKAB和Vattenfall的Hybrit計畫、Salzgitter 的GrInHy 和 SALCOS以及thyssenkrupp領導的H2morrow項目等均是氫冶金技術研發專案。雖然氫冶金擁有巨大的節能降碳潛力,但目前仍處於研發起步階段,面臨眾多嚴峻挑戰。除了氫冶煉技術尚不成熟外,氫冶煉所需之綠氫,需要高度仰賴風力、太陽能等可再生能源電力。一公噸的氫能直接還原鐵約需90公斤的氫氣,若要將全球每年約14億公噸之高爐/轉爐流程所生產的粗鋼,都轉換為氫能直接還原製程,每年約需要氫氣1.26億公噸。要大規模、低成本生產綠氫,尚面臨許多難題,連帶會影響未來氫能煉鐵產能的擴充步伐。
(三)碳捕捉、再利用與封存(CCUS)技術研發
由德國聯邦教育及研究部資助,ThyssenKrupp等15家企業合作執行的Carbon2Chem計畫是碳捕捉與再利用的典型案例。Carbon2Chem是利用煉鋼廠CO2廢氣生產含有C、H元素的合成氣體,進而生產氨氣、甲醇等初級化工產品。臺灣中鋼公司亦於2022年投資2億元建置國內首座「鋼化聯產」先導示範工場,結合技術處科技專案補助工研院的碳捕捉再利用技術,進行碳循環再利用的技術驗證。示範工場計畫驗證商業模式成功後,將共同成立碳循環經濟園區,預估年減碳量可達290萬噸。CCU技術與氫冶金技術一樣,正處於試驗研發的起步階段,還未大規模投入工程應用。目前全球有多項研發和試點項目進行中,包括:HIsarna、Al Reyadah、Carbon2Chem、Steelanol和COURSE 50等。惟CCU僅可發揮碳中和的過渡性任務,但無法成為淨零碳排的最終解決方案。
(四)清潔能源利用
美國Nucor鋼鐵在密蘇里州建成全美首座100%使用風能發電的煉鋼廠,Evraz Group北美公司將旗下洛磯山煉鋼廠改造成全美首座100%太陽能發電的煉鋼廠。2026年ThyssenKrupp位於杜伊斯堡的直接還原工廠落成後,將使用綠色氫和可再生電力,其第一座直接還原鐵產能達250萬噸。還有許許多多的鋼廠,均大量建置風電、太陽能發電設備,以降低二氧化碳排放。以國內中鋼集團為例,其太陽光電系統已建置達87.3MW,另投入開發離岸風場300MW,預計113年完成建置,屆時每年發電量約為12億度,減排約61萬噸二氧化碳當量/年。【表1】為彙整之全球主要低碳鋼鐵生產專案/技術一覽表,包含計畫的參與機構、專案/技術名稱。
表1 全球主要低碳鋼鐵生產專案/技術一覽表
國家/地區 |
參與機構 |
低碳專案/技術名稱 |
美國 |
美國能源部、美國鋼鐵協會 |
1.鋼鐵生產及低碳煉鋼CO2排放新技術
2.鐵礦石熔煉氧化電解技術
3.氫基還原煉鐵閃速熔煉技術
|
Nucor公司 |
100%風能發電煉鋼項目 |
Evraz 集團、美國電力公司 |
100%太陽能煉鋼項目 |
日本 |
日本鐵鋼聯盟 |
COURSE50 |
日本鐵鋼協會 |
Zero emission power generation technology |
韓國 |
韓國產業通商資源部 |
COOLSTAR |
POSCO |
與Primetals簽署意向書,將在韓國開發氫基生鐵生產示範廠HyREX |
歐盟 |
歐洲鋼鐵技術平台(ESTEP) |
ULCOS |
德國 |
ThyssenKrupp公司 |
Carbon2Chem、tkH2Steel (H2Stahl)、H2morrow |
Salzgitter、Tenova |
SALCOS(基於Energiron技術建造DRI設備) Energiron是創新的HYL直接還原技術 |
ArcelorMittal |
MIDREX H2 |
瑞典 |
SSAB、LKAB、Vattenfall |
HYBRIT |
H2 GREEN STEEL |
SMS SIEMAG設備 |
奧地利 |
Voestalpine、Siemens AG、Verbund |
H2FUTURE |
Voestalpine、K1-MET和 Montanuniversität Leoben |
SuSteel |
臺灣 |
經濟部、中鋼、工研院 |
鋼化聯產 |
芬蘭 |
Vanir Green Industries 、Blastr Green Steel |
Blastr Green Steel |
英國 |
TATA Steel英國公司 |
科學基礎減量目標倡議(SBTi) |
荷蘭 |
TATA Steel荷蘭公司 |
Energiron 直接還原工廠 |
法國 |
GravitHy、Primetals、Engie、Plug、Forvia等 |
GravitHy直接還原工廠 |
資料來源:金屬中心MII-ITIS研究團隊整理(2023/03)
三、未來新興煉鐵技術動向
目前世界鋼鐵業探索與試點的低碳技術,例如:氫能煉鐵、碳捕捉再利用與封存(CCUS)等技術有其缺點,例如:氫能煉鐵存在多種風險,如何取得成本低廉之綠氫;又如CCUS技術,仍會排放大量溫室氣體,除非採用生物能源與碳捕獲和儲存(BECCS)或使用直接氣體捕捉(DAC),這些都會顯著增加減碳成本。因此,持續探索低成本的新型清潔煉鐵技術是一個持續性的重要目標。除了淨零碳排和實現低成本的目標之外,新的煉鐵技術也必須提供可靠的技術途徑,以促成全球鋼鐵業的大幅度去碳化。
目前全球鋼鐵業探索的代表性新煉鐵技術有:氫電漿熔融還原煉鐵、電解煉鐵、生質能煉鐵、新興熱化學煉鐵等。
(一)氫電漿熔融還原(hydrogen plasma smelting reduction, HPSR)煉鐵
該技術以氫電漿用為還原劑,而不是氫氣。以氫氣還原鐵礦石是吸熱的化學反應,必須另外提供熱量來進行還原反應。氫電漿比氫氣含有更高能量,氫電漿還原鐵礦石是放熱反應,且氫電漿與鐵礦石的反應速度更快。奧地利Voestalpine AG與Leoben大學已合作研究多年,但尚未進行全面的試驗工作。其他煉鐵技術路徑相比,氫電漿煉鐵可被視為是氫能直接還原煉鐵的競爭者,兩者的投入原料均為氫,該兩種技術面臨的挑戰類似,均依賴淨零碳排放的綠氫生產。
(二)電解煉鐵
電解鐵礦石不需要額外的還原劑,因為整個反應是鐵礦石的「自身氧化還原反應」,該反應由電力驅動並在電化學電池中進行,其中在陰極產生Fe,在陽極產生氧氣。電解煉鐵的一個主要好處是,無需使用任何中間還原劑(如:煉焦煤、氫氣、天然氣),可以提高能源效率。電解煉鐵的最大技術挑戰是生產規模,因為Fe生產速率取決於電極表面區域輸送的電流。以電解法生產鋼鐵的另一個挑戰是鐵礦石中存在的雜質,若這些雜質具有與Fe相似的密度和溶解度特性,則雜質可能會混入最終的鐵錠中,此一現象可能有利、可能有害,具體取決於雜質元素和所需的合金產品。目前電解煉鐵技術路徑主要分為兩類:高溫電解(> ~1500 °C)和低溫電解(< ~110 °C),中溫煉鐵在經濟性被認為是次優的,因此略過不談。
1.高溫電解熔融煉鐵:高溫過程的好處是更快的熱動力學,意味更快的生產速率。2004 ~2012年間ArcelorMittal投入MIDEIO ULCOS技術的研發。而美國Boston Metal則將麻省理工學院的相關研發進行商業化。高溫電解的主要挑戰是資本支出相當高,耐火材需要容納高溫熔體,並承受高溫和腐蝕環境。此外,製程需通大量電流,意味電力設備成本、耗電很高。為實現連續式電解生產,也必須維持熔體高溫,工廠須使用基載電力。而惰性、非腐蝕性陽極可能會變得昂貴。為了解決這些挑戰,研究製造更便宜的耐火材料、惰性陽極、高能效電力總成、模組化電解反應器等,均是未來的可能商機。
2.低溫電解熔融煉鐵:低溫運行的電解氧化還原反應,可能具有能源消耗較低的好處,因為不需要耐火材料,設備成本較低。此一技術可以實現靈活生產,可利用離峰低電價進行生產。由ArcelorMittal設立的SIDERWIN示範計畫,是一種低溫電解技術,用於批次生產鐵金屬板。低溫電解煉鐵的主要挑戰是反應速度較慢。可間歇性生產雖然有利於降低電力取得成本,但設備利用率會因此降低,從而增加鋼鐵生產成本。
(三)生質能煉鐵
此一技術使用生質能衍生的還原劑原料,替代現有化石原料。生物炭可以替代高爐中的煉焦煤,也可利用某地可取得的生質能,修改煉鐵爐反應器之設計,以靈活搭配不同地區的生質燃料。木材是早期人類煉鐵的重要還原劑,人們對使用生質燃料煉鐵的興趣重新抬頭,主要還是受到去碳化議題之影響,但生質能將已封存的碳重新又排回大氣,這種生質能鋼可能不被認為是碳中和鋼材。
(四)新興熱化學煉鐵
使用非化石、非生質能燃料的熱化學煉鐵可能是鋼鐵業碳中和的一項選擇。電解煉鐵受到電極表面積之限制,產量可能受限,但熱化學反應爐反應面積大,可能獲得更高的生產速率。在可再生合成氣體的案例中,該技術將通過使用可持續合成氣體,建立合成氣DRI製程(NG-DRI)。使用可再生能源將捕捉的CO2轉化為CO,釋放O2副產品。該技術的優點是天然氣DRI煉鐵技術已經成熟,只需要對CO2循環進行設備改造及合成氣進行研發。目前使用非化石、非生物替代還原劑,進行熱化學煉鐵的研究相對不足,需要更多研究來確定哪些原料可以大規模有效利用。
(本文作者為金屬中心執行產業技術基磐研究與知識服務計畫產業分析師)
點閱數:
5293