:::
科研案例
精準控制加熱變形 金屬零件再小也不怕!
發佈日期:2022-11-02
案例摘要:
在經濟部技術處科技專案支持下,金屬中心創全球之先,開發微型元件熱處理設備,大幅提升良率,更榮獲2021年全球百大科技研發獎(R&D 100 Awards)和美國愛迪生獎銅牌(Edison Awards)肯定。
內容說明:
金屬中心 ▶ 全球首創微型元件熱處理設備
技術特色
打造專門適用小於2毫米微型零件的熱處理設備,並設計特殊的螺旋吸力裝置,讓收料率達100%。
產業擴散
設備導入祥儀、興光等廠商,促進投資逾2.3億元,更成功切入國際車輛大廠的零組件供應鏈。
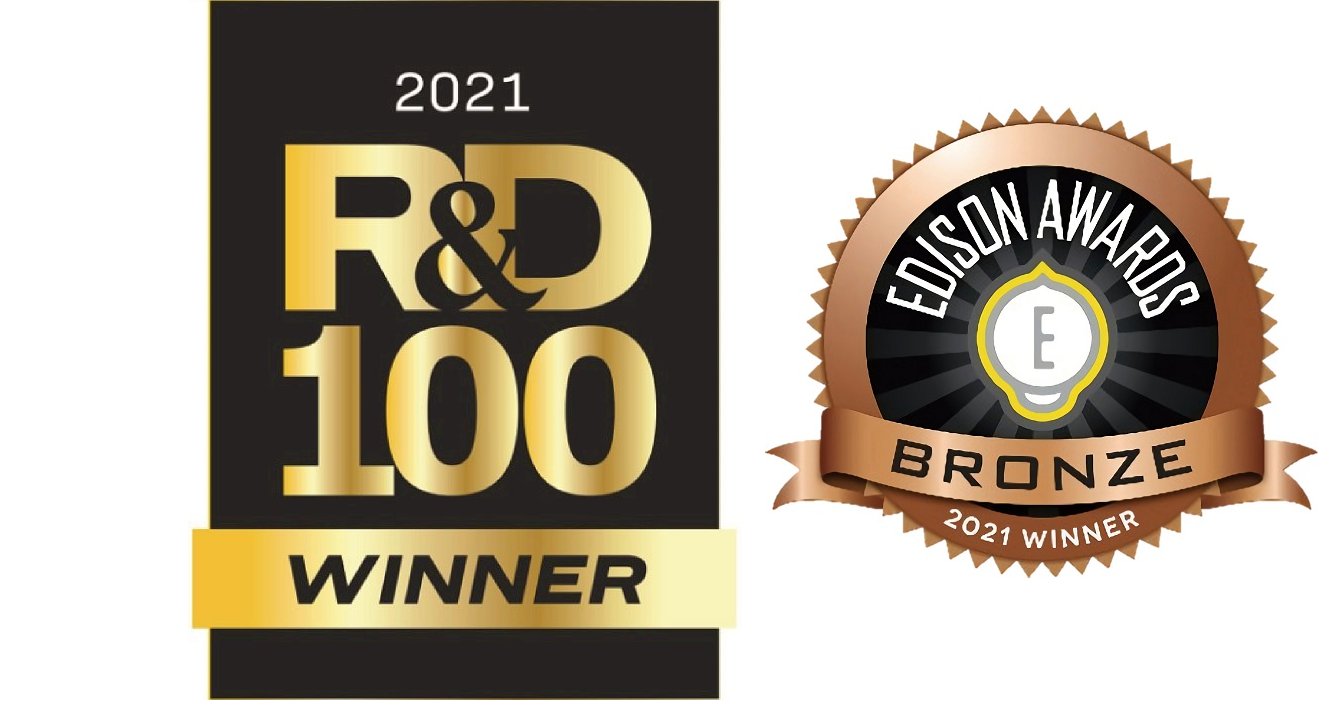
一顆顆微小的螺絲、齒輪,迷你尺寸幾乎肉眼難辨,卻是讓馬達、3C產品等設備運轉如常的關鍵零件。過去微小零件進行熱處理加工時,容易發生受熱不均、無法完整收料等問題,在經濟部技術處科技專案支持下,金屬中心創全球之先,開發微型元件熱處理設備,大幅提升良率,更榮獲2021年全球百大科技研發獎(R&D 100 Awards)和美國愛迪生獎銅牌(Edison Awards)肯定。
「熱處理是工業之母!」金屬中心副組長黃家宏表示,為了提升金屬的強韌性,必須加熱改變組織結構,加強硬度,在生產中至關重要。但不管多麼精密的熱處理設備,工件加熱一定會變形,端看能否控制在可接受的範圍內。
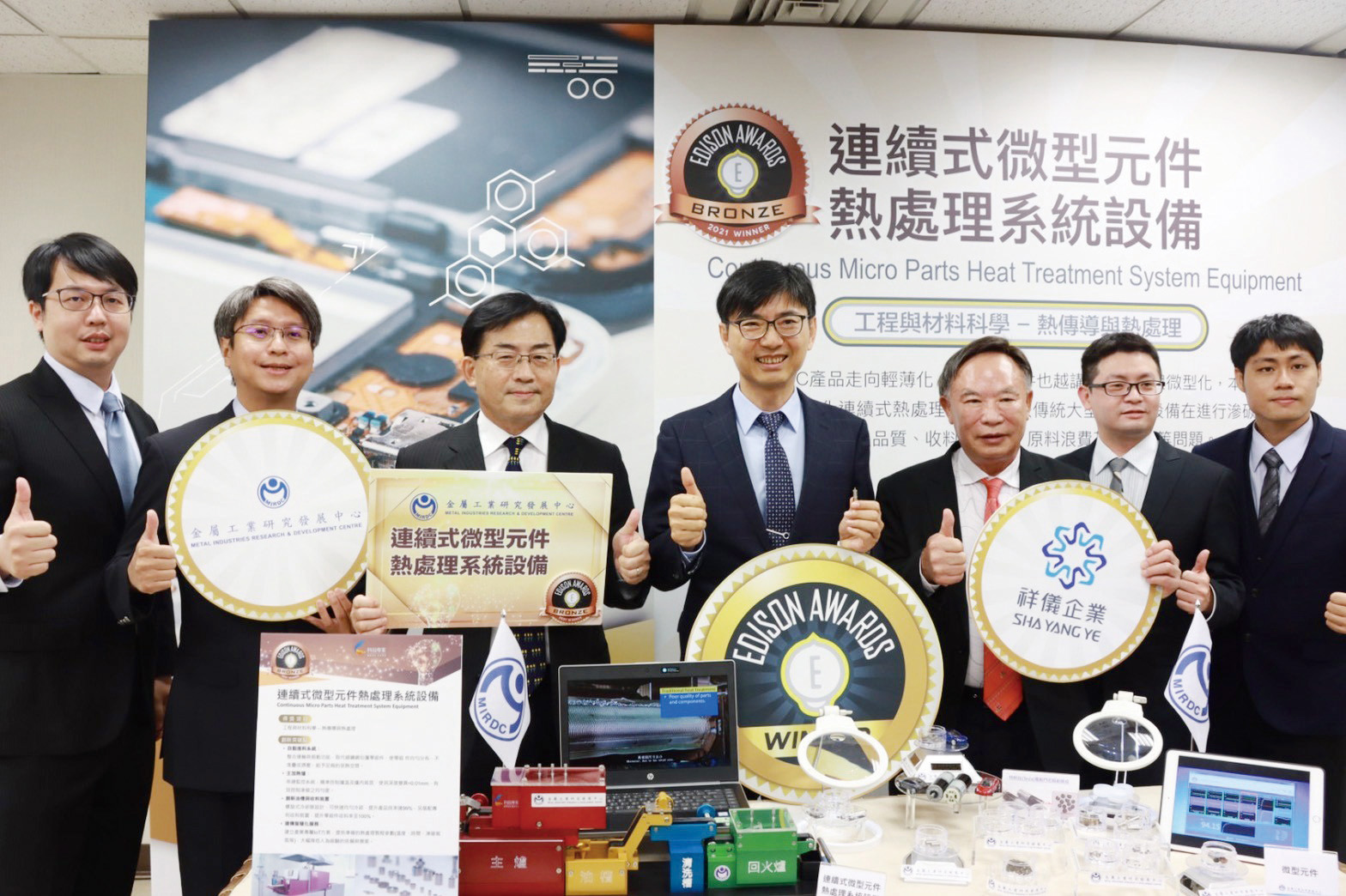
▲ 金屬中心開發的連續式微型元件熱處理設備,榮獲2021年全球百大科技研發獎、 美國愛迪生銅獎雙重肯定。
打造特殊螺旋吸力裝置 收料率達100%
由於微型零件小而輕,金屬中心工程師劉俊呈指出,業者多半會用不鏽鋼網袋打包,置於淬火油槽中加熱,「大約一個拳頭大小」。但這會導致零件堆疊、受熱不均,無法精準控制變形量;若是不用網袋包覆,收料時宛如大海撈針,流失率大增。
為此,研發團隊開發針對微型零件的小型加熱爐,在收料步驟,則設計專利的螺旋吸力裝置,透過吸力讓微型零件快速沉入油槽底部,再掉入收集箱,可完全捕集四處分散的微小零件。
這有兩個優點,第一是解決收料問題,收料率從60%提升至100%;第二是提升良率,過去微型零件因過於輕巧,常浮在油槽表面,現今透過吸力讓零件完整沉浸在淬火油中,良率從70%提升至99%,更進而提升產品使用壽命2~5倍。
國產替代進口 助廠商切入國際供應鏈
金屬中心從10年前開始投入,設備已進化到第四代。對比國外熱處理設備售價高達新臺幣1,500~2,000萬元,卻僅有單一淬火功能,也只能用於銅合金;金屬中心第四代設備則適用於碳鋼、合金鋼、不鏽鋼等國內業者常用的材料,並具備加熱、淬火、收料、清洗、回火等連續步驟,同時導入可視化監控模組,收集製程參數,將變形誤差從5%縮小到1%,可取代國外設備,達成國產自主性。
目前設備已導入全球前三大精密元件廠祥儀,原先祥儀委由外部熱處理代工廠負責,作業期長達30~45天,現在有了自家設備,只要1、2天就能加工完畢。
劉俊呈透露,最早設備還在試驗階段時,祥儀正好接到日本手工具大廠Makita的打樣測試,先前委外代工廠試作超過半年都無法達到要求,到了客戶要返回日本當天,金屬中心緊急接下任務,早上拿到樣品、下午就試做完成,順利促成祥儀簽下3,000萬元訂單。有了微型元件熱處理設備助攻,後續祥儀也成功切入特斯拉、Bosch、賓士等國際大廠的零組件供應鏈。
「以往祥儀企業委由外部熱處理代工廠負責,作業期至少一個月起跳,現在有了自家設備,只要1、2天就能加工完畢,可快速回應客戶需求。」
這套設備也導入熱處理代工廠興光,促成興光取得日本精密馬達廠萬寶至的訂單。整體來說,透過擴散產業界應用,創造技術移轉和工業服務金額超過4,300萬元,促進投資逾2.3億元,驅動臺灣精密製造業競爭力再升級。
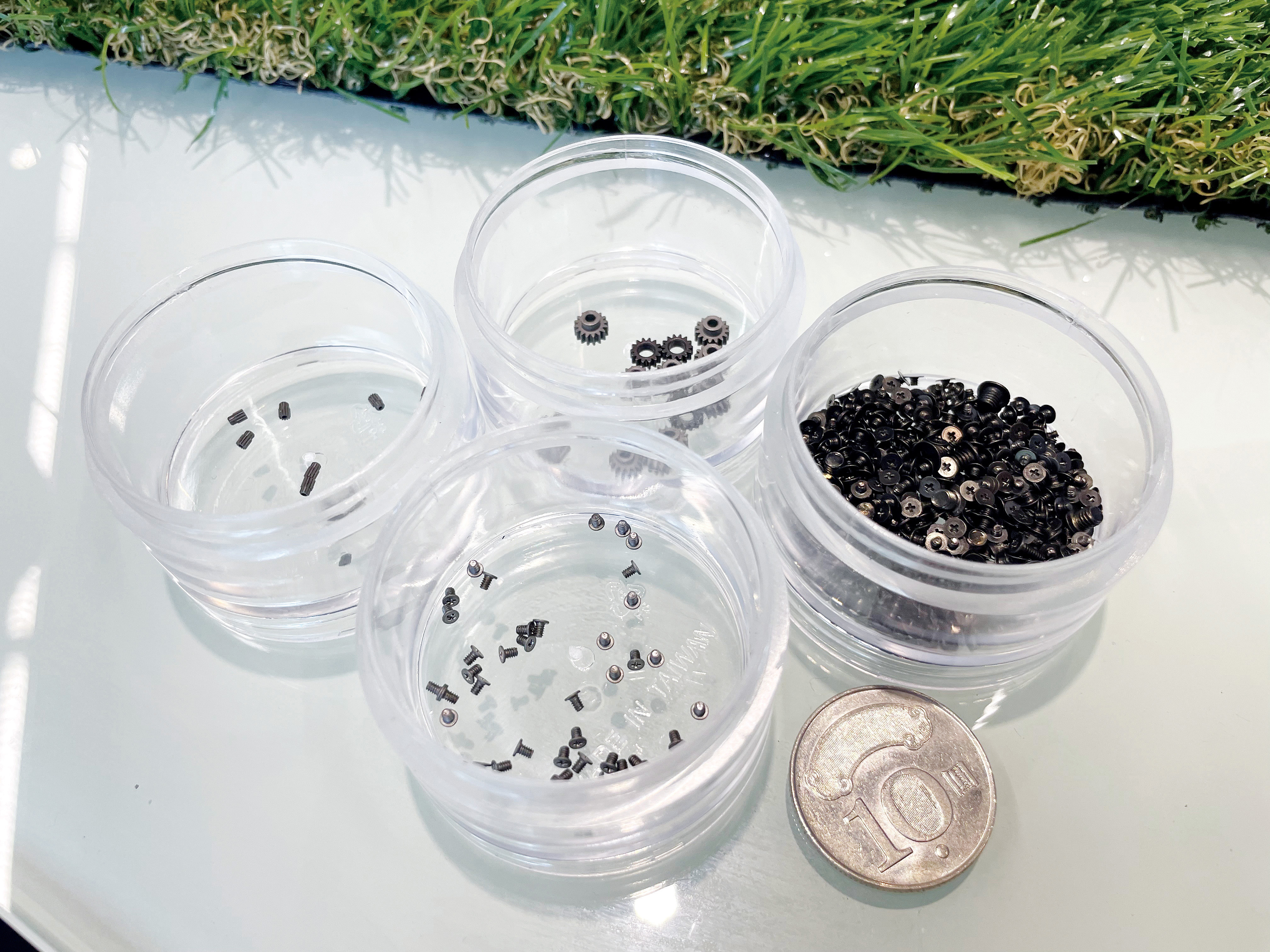
▲ 金屬中心自主研發連續式微型元件熱處理設備,專用於2毫米以下的微小零件。
點閱數:
909