:::
科技新知
基於數位雙生(Digital Twin)的工具機精度補償
發表日期:2024-08-28
作者:陳佳盟(工研院)
摘要:
具備所需的精度進行加工是對工具機的基本要求。由於機器人技術(包括影像辨識和控制方法以及工件傳送方法)的最新進展,無需人工協助的連續製程和工廠利用率不斷增加;在這種操作條件下,保持加工精度以確保產品品質非常重要。
全文:
一、前言
具備所需的精度進行加工是對工具機的基本要求。由於機器人技術(包括影像辨識和控制方法以及工件傳送方法)的最新進展,無需人工協助的連續製程和工廠利用率不斷增加;在這種操作條件下,保持加工精度以確保產品品質非常重要。刀具磨損和工具機結構熱變形是連續運轉中加工精度惡化的關鍵因素,特別是在加工過程中,由切削熱、主軸和移動軸馬達引起的熱變形是不可避免的。熱量是降低加工精度的主要因素,估計約占總加工誤差的70%。
為了減少熱位移,有研究團隊採用了以下措施,包括熱源冷卻、熱源隔離、低熱變形結構、熱對稱、溫度控制和補償;也有研究人員根據溫度數據,採用ARX(Autoregressive Exogenous input)模型、神經網路、機器學習等方法,以精確補償刀具與工件之間的相對位移。但沒有考慮機器結構的幾何形狀、材料性能等物理特性,因此無法辨識引起機械結構熱位移的機制和因素。熱流體分析作為一種基於物理性質的預測,可以利用有限元素分析或有限體積法來獲取機器周圍的溫度場並預測機器結構的變形;然而,由於分析所需的時間,此方法不適合預測短時間內的熱變形。為了省略熱流體分析中的計算時間,提出了利用感測器陣列測量機械結構內溫度分布的方法,利用這些熱負荷數據,透過有限元素計算和補償熱變形。這種方法使用廉價的感測器,但在現有機器上安裝它們並不容易,因為許多感測器需要安裝在機器主體周圍和內部以及蓋子後面。
本文開發了一種數位雙生技術,利用機器結構幾何形狀、工件和刀具幾何形狀以及材料屬性,基於物理模擬來預測加工中的動態特性;研究結果發現加工預測結果與實際工具機的切削振動現象非常吻合。利用此方法可以在短時間內計算出機械結構的熱變形,且此方法結合動力學和熱模型的新型加工空間精度預測和補償技術,利用工廠環境、主軸冷卻、加工室的環境溫度,可以預測熱變形,更可以全面、數位化地再現工具機的行為,不僅包括熱變形,還包括動態切削振動,從而實現工具機更準確、高效、穩定的運行。
二、數位雙生模型建立
本章節介紹如何建立基於工具機結構物理模擬的動態和熱變形數位雙生模型;這些數位雙生模型是基於相同機器結構的幾何形狀和材料特性,且將分為以下兩部分:高採樣率下描述加工過程的動態數位雙生模型和低採樣率下分析結構變形的熱數位雙生模型。整合的數位雙生模型是透過耦合這些模型來進行創建:
(一)動態數位雙生模型
為了描述動力學,使用有限元素建模的工具機被分為多個子結構,例如刀具、刀柄和主軸,並將這些子結構組合起來以創建模型。為了計算各子結構的特徵值,得到各子結構在模態座標系中的運動方程式。
(二)熱模型
在熱變形的數位雙生模型方面,應用有限元素模型的KMS(Krylov和模態子空間)簡化來考慮機械結構的幾何形狀和材料特性,並透過應用估計的傳熱係數,即可避免熱流體分析。
三、數位雙生模型參數識別
前面所介紹的動態和熱位移估計的數位雙生模型將應用於工作台尺寸為630 mm的原型 五軸臥式加工中心,以估計其行為並將其與真實機器進行比較。我們發現機器的環境溫度在溫控室中在(4h-1h-4h)的時間跨度內改變8°C,如圖1a所示。利用四個溫度資料以確認機械結構各邊界的傳熱係數和對流溫度變化係數;四個溫度資料包括工具機環境溫度、加工室內部溫度、床身內部溫度、主軸及工作台冷卻溫度,如圖1所示。
使用約二十個感測器直接連接到機器結構上,以測量溫度結果。分析模型經過反覆計算發現分析結果與機器結構初步測試結果吻合,如圖2所示。分析結果準確地捕捉了實際行為,也透過比較接觸式探針的測量結果和模擬結果來評估位移預測的準確性,如圖3所示。該方法也準確地重現了圖4中指定位置的熱變形;而這些熱位移可以在大約10分鐘內即可計算出來。
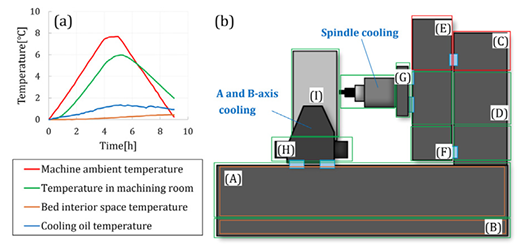
資料來源:Digital twin based accuracy compensation (2023/05)
圖1 機器結構參考溫度(a)與熱傳係數邊界區域分類(b)
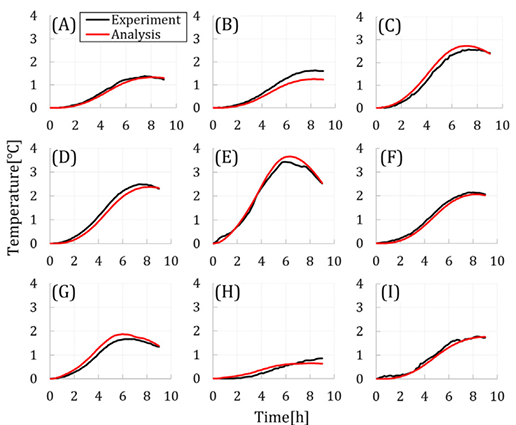
資料來源:Digital twin based accuracy compensation (2023/05)
圖2 基於熱傳係數估算圖1(b)中各區域(A)»(I)的溫度變化
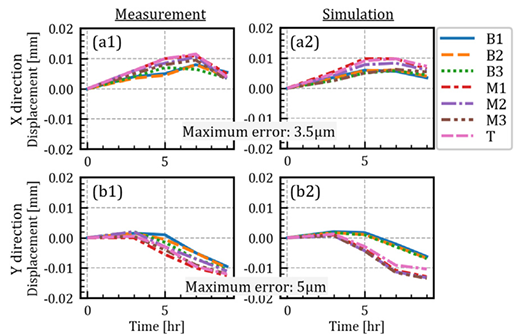
資料來源:Digital twin based accuracy compensation (2023/05)
圖3 熱位移重現評估結果與圖4中Bi、Mi和T處的接觸探針測量結果進行比較
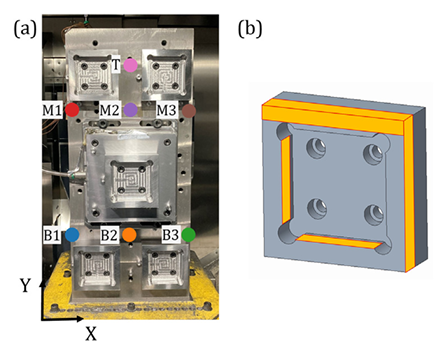
資料來源:Digital twin based accuracy compensation (2023/05)
圖4 安裝在夾具上的五個量測位置(a)與用於加工驗證的工件(b)
四、使用數位雙生進行精度補償
透過計算加工空間內的誤差並將補償量與指令值相加來進行加工驗證。誤差是根據工具機環境溫度、加工室內部溫度、床身內部溫度以及主軸和工作台冷卻溫度計算得出,如圖4所示,工件安裝在夾具上的五個位置。這樣可以評估X軸行程為360 mm、Y軸行程為700 mm的加工空間中的加工精度。為了測量切削力,將測力計(Kistler 9255C)安裝在工件的中心。
利用數位雙生的預測結果來補償溫度變化條件下的熱位移,且機器的環境溫度變化與第三節相同。在立方體工件型腔的四個內側面和兩個外側面的六個位置進行加工,如圖4(b)中橙色所示;切削條件如表1所示。
表1 精度補償評估的切削條件
參數 |
數值 |
立銑刀直徑 |
16 mm |
齒數 |
4 |
主軸轉速 |
2,000 rpm |
進給速度 |
480 mm/min |
軸向切削深度 |
20 mm |
徑向切削深度 |
0.1 mm |
資料來源:Digital twin based accuracy compensation (2023/05)
加工精度的評估是透過接觸式測頭以每邊17.5mm的間隔在5點測量工件型腔的內側來進行;此外,也比較了補償前後的精確度。加工中段中心工件時,使用測功機來測量切削力。
圖5是從工件側觀察補償前後5個位置的測量結果。圖中所示數據是在補償前熱位移達到最大時(7 h)時記錄的。透過補償,10 μm和15 μm的位移顯著減小到1 μm和3 μm。
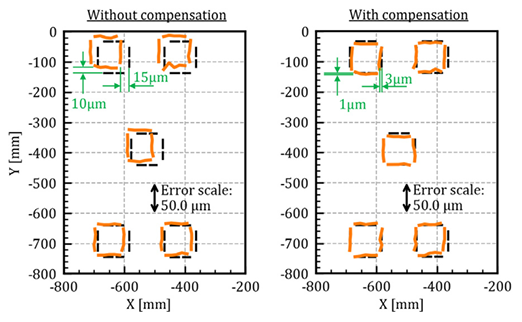
資料來源:Digital twin based accuracy compensation (2023/05)
圖5 加工空間中的熱位移補償結果
圖6(a)顯示工件中心加工過程中測量的切削力,圖6(b)顯示模擬結果。預先根據測量的切削力來決定切削係數,測試時使用熱壓配合刀具,刀尖跳動約4毫米。在數位雙生模擬中考慮跳動以計算動態切削力。如圖6所示,測量的切削力和模擬的切削力非常一致,包括由於每轉跳動而導致切削力的變化。
由上述研究可知,動力學和熱行為的數位雙生使得估算工具機結構的熱變形成為可能。透過補償所提出的方法估計的誤差,可以提高切割精度;此外,還可以估計動態行為,包括刀具跳動的切削力。
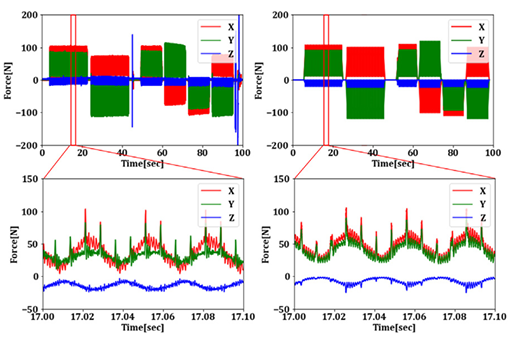
資料來源:Digital twin based accuracy compensation (2023/05)
圖6 實際與數位再現的動態切削力比較
五、結論
本文提出了一種利用具有動態特性和熱行為的綜合數位雙生技術來補償加工精度的新方法,其中不僅包括工具機結構的熱變形,還包括動態切削力。有限元素模型的簡化使得可以加快估計溫度分布的計算時間;此外,採用對流溫度變化係數可以僅使用機器結構內部的四個溫度感測器來預測熱位移。本文之研究方法能夠製造高精度、高效率、運作穩定的工具機;此外,該方法還有助於建造更先進的工具機,可以在長時間連續運行期間監控和自我優化加工過程。
近年來,歐洲工具機廠也開始運用數位雙生技術加速生產流程,如機台設計CAE模擬將機構、電氣與自動化系統從以往分散開發,改以數位化平台建立虛擬機台模型而加速初期開發流程,並開始支援新機台數位設計優化,以虛擬試運轉節省工具機製造商開發時間。以全球工具機龍頭DMG MORI為例,生產工具機的直接碳排放量只占整個生產過程的7%,但將供應商製造工程囊括進來的話,零件採購部分卻占整體的70%。因此由企業內部逐漸擴展至下游供應鏈,包括再生能源與相關配套機制,能源即服務解決方案興起及以生產效率帶動節能減碳,才有可能共創零碳生態系。德國控制器大廠西門子也提出SINUMERIK ONE,其透過虛擬控制器、操作面板、PLC、SimDrive、3D模擬等工具進行工具機數位雙生建置,提供機台虛擬測試與調校,加速綠色工具機虛擬整合製造技術發展。
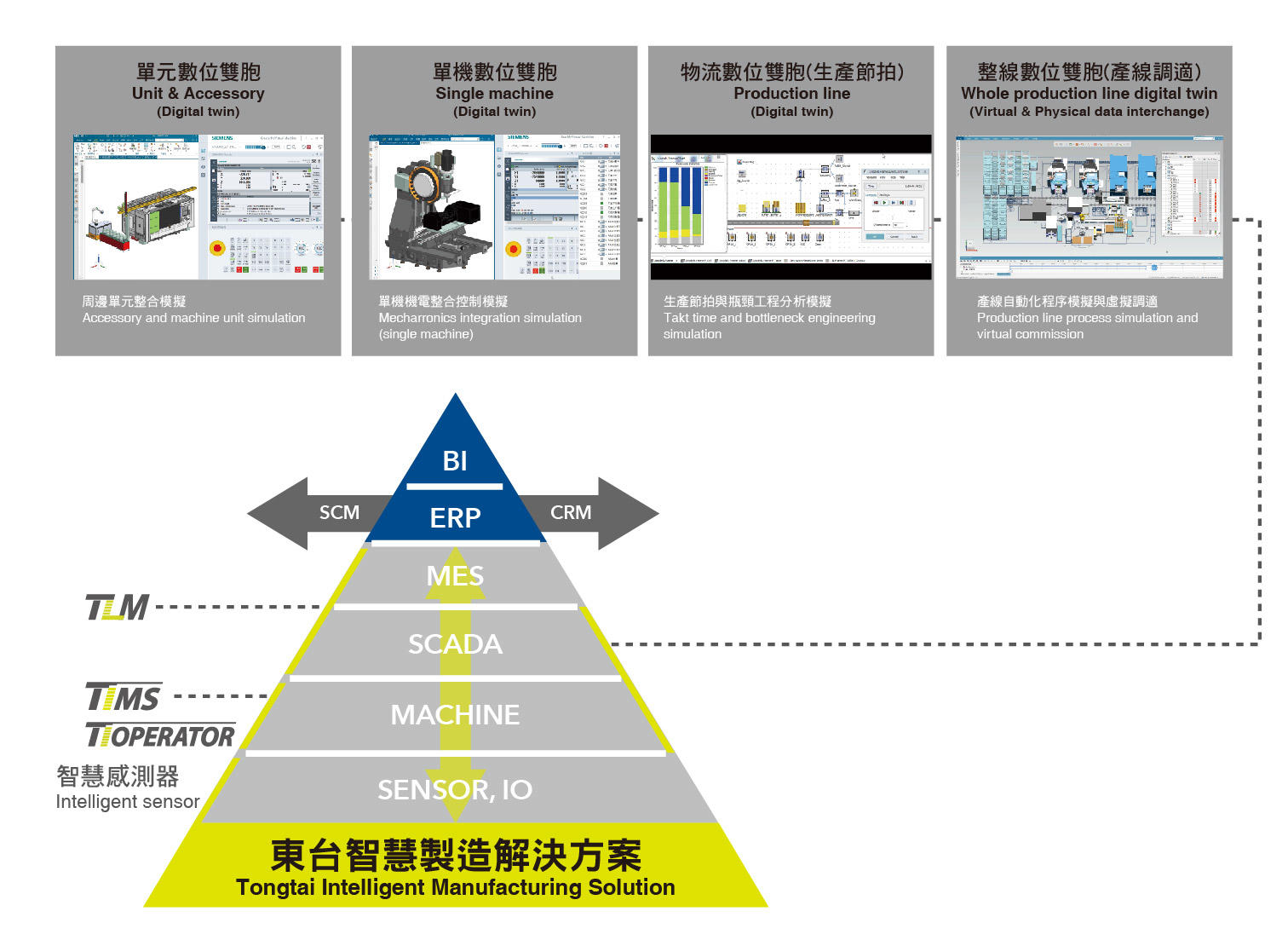
資料來源:東台精機(2024/06)
圖7 東台所推出之各式數位雙生(數位雙胞)技術
國內廠商方面,東台精機標榜全系列機種均提供數位雙生技術,從機台開發規劃初期便導入數位雙生技術,如圖7,不論在單機生產、流水線加工、甚至自動化線及物流規劃分析等,以協助客戶解決潛在問題與降低投資風險。數位雙生技術預料將是未來製造的趨勢、必定發展的方向,值得廠商積極投入、加大布局。
(本文作者為工研院產科國際所執行產業技術基磐研究與知識服務計畫產業分析師)
點閱數:
464